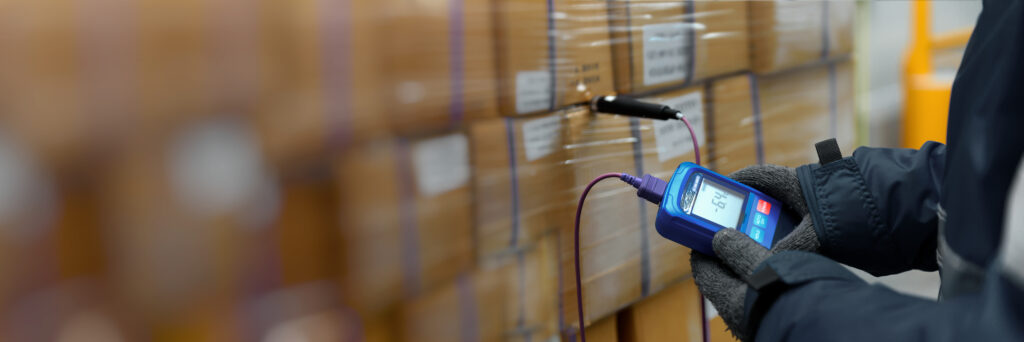
NanoSlick Tungsten Disulfide Lubricants for Extreme Temperature Environments
When the conditions are extreme, industries around the globe need high-performance lubricants that can handle the strain and stay tenacious in the toughest of environments. For many industrial applications, NanoSlick Tungsten Disulfide Lubricants are becoming a
world-renowned leader, offering unprecedented levels of protection and lubrication when facing extreme temperatures and heavy loads.
In this guide, we will discuss how our Tungsten Disulfide lubricants can be used for extreme temperature environments, what makes them so effective, and how to best use them for maximum performance. We will also look at some of the challenges that these lubricants face, such as wear and tear over time, and how to maintain them for optimal operation.
1. Advantages of NanoSlick Tungsten Disulfide Lubricants
Tungsten Disulfide Lubricants offer many advantages when it comes to extreme temperature environments.
One of the biggest advantages is that the lubricants can handle high temperatures. This means that they can be used in areas where other lubricants would not be able to.
Our lubricants are also resistant to corrosion. This means that they can be used in areas where other lubricants would not be able to.
Our lubricants are also resistant to wear and tear. This means that they can be used in areas where other lubricants would not be able to.
2. Applications of NanoSlick Tungsten Disulfide Lubricants in Extreme Temperature Environments
NanoSlick Tungsten Disulfide lubricants are commonly used in extreme temperature environments due to their ability to resist wear and tear.
Applications of NanoSlick Tungsten Disulfide Lubricants in Extreme Temperature Environments:
NanoSlick Tungsten Disulfide lubricants are commonly used in extreme temperature environments due to their ability to resist wear and tear. They are used in applications such as oil and gas production, mining, aerospace, and automotive. Tungsten Disulfide lubricants are also used in applications where extreme temperatures are a consideration, such as in the food and beverage industry.
3. Assessing the Performance of NanoSlick Tungsten Disulfide Lubricants
When it comes to extreme temperature environments, nothing works better than NanoSlick tungsten disulfide lubricants (NTDSLs). TDSLs are the gold standard for lubrication because they have a very low coefficient of friction and provide long lasting lubrication in extreme cold and hot environments.
While there are other types of lubricants that can be used in these environments, NTDSLs are the best option because of their performance.
To assess the performance of NTDSLs, it is important to understand the different factors that can affect lubrication. These factors include the lubricant type, the operating conditions, and the type of surface being lubricated.
To ensure that NTDSLs are the best option for a given application, it is important to understand these factors. By doing so, you can ensure that the lubricant is used in the most effective way possible.
4. Factors to Consider When Choosing NanoSlick Tungsten Disulfide Lubricants
When it comes to selecting the right lubricant for your extreme temperature environment, there are a few factors you need to consider.
The first is the temperature range you need to cover. Tungsten disulfide lubricants can handle a wide pressure range, from 0 to 300,000 PSI.
The third is the type of load you need to support. NanoSlick Tungsten disulfide lubricants are designed for applications that require high loads and high temperatures.
So, when you are selecting a lubricant for your extreme temperature environment, make sure to take all of these factors into account.
Conclusion
In conclusion, NanoSlick tungsten disulfide lubricants are an excellent solution for extreme temperature environments. They offer unmatched durability, heat resistance, and low friction characteristics. Choosing the right lubricant is key to ensuring maximum equipment performance and longevity. By using NanoSlick tungsten disulfide lubricants, you can significantly reduce wear and extend the life of your equipment. So why wait? Make the switch today and experience the benefits firsthand. Contact us now to learn more about our tungsten disulfide lubricants!
FAQ
What are the advantages of NanoSlick tungsten disulfide lubricants?
Some of the advantages of our tungsten disulfide lubricants are that they are resistant to oxidation and wear, have a high shear strength, and have a long life.
What are the applications of NanoSlick tungsten disulfide lubricants in extreme temperature environments?
NanoSlick Tungsten disulfide lubricants are widely used in extreme temperature environments because they have excellent extreme temperature properties. They can withstand high temperatures and are resistant to wear and tear. They are also non-toxic and environmentally friendly.
How can I assess the performance of NanoSlick tungsten disulfide lubricants?
There are a number of ways to measure the performance of our tungsten disulfide lubricants in extreme environments. One way is to measure the load life of a part. This can be done by measuring the time it takes for the part to wear out or break.
What are some tips for choosing the best NanoSlick tungsten disulfide lubricants for my specific application?
When choosing a tungsten disulfide lubricant, it is important to take into account the specific application. Some factors to consider include the material’s temperature range, oil viscosity, and lubrication properties. Additionally, it is important to determine the lubricant’s compatibility with the material and the operating conditions.
What are the factors to consider when choosing NanoSlick tungsten disulfide lubricants?
Tungsten disulfide lubricants are a popular choice for high-temperature environments, due to their ability to provide long-term lubrication and high wear resistance. Some factors to consider when choosing tungsten disulfide lubricants include the lubricant’s properties (such as viscosity, thermal stability, and corrosiveness), the application area, and the lubricant’s compatibility with other components.